
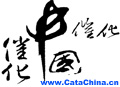
http://202.113.13.67/courses/chemtech/edutools.php?tid=342
《化工工艺》精品课程“氯化过程”部分——天津大学(本人备用)
9.1 概 述 氯化过程的主要产物是氯代烃,氯代烃是指烃的氯取代化合物,即脂肪烃、脂环烃和芳烃中的一个或多个,甚至全部氢原子被氯原子取代生成的化合物。由于氯原子的引入,改变了原来烃的性质。氯代烃的化学性质比较活泼,因此,在工业上有着广泛的用途。
氯代烃是科学发现和工业应用较早的化合物,重要的工业氯代脂肪烃包括氯乙烯、1,2-二氯乙烷、二氯乙烯、一氯甲烷、二氯甲烷、三氯甲烷、四氯化碳、1,1,1-三氯乙烷、三氯乙烯、四氯乙烯、氯化石蜡、氯乙烷、氯丙烯、氯丁二烯和氯乙醛、氯乙酸等。
氯代烃的主要应用领域有两个。-是用作溶剂,例如用作干洗剂、电子工业清洗剂、金属清洗剂、粘合剂及涂料的溶剂、萃取剂等。二是用作合成大量有机产品及精 细化工产品的中间体和聚合物的单体,例如合成制冷剂、烟雾剂、农药、医药、染料、纺织助剂等的中间体、聚合物的单体。
9.2 氯代烃的主要生产方法 用于氯代烃生产过程的化学反应主要包括取代氯化、加成氯化、氢氯化、氯解、热裂解、脱氯化氢和氧氯化等,其中,取代氯化、加成氯化和氧氯化是主要方法。
1 取代氯化
以氯取代烃分子中的一个或几个氢原子生产氯代烃,是最重要的工业氯化过程。该过程可在气相或液相中进行。取代氯化反应是强放热反应,碳键结构和被取代氢原 子的位置对反应热影响不大。 反应的关键是得到活泼的氯,可以通过热、光及自由基引发的方法。热氯化在气相进行,温度通常在250℃以上。由于简单、经济,使用最广。光氯化反应常用波 长为300~500nm的紫外线作为光源。自由基引发可以采用偶氮化合物作为引发剂。光和自由基引发的取代氯化过程一般在液相进行,反应条件比热氯化温 和,选择性好。取代氯化反应按自由基机理进行。
因此,取代氯化一般不可能生成单一的氯代烃,多氯代烃也同时生成。一氯代烃对多氯代烃的比例与反应原料中烃对氯的摩尔比有关,因此,工业上采用改变烃与氯 的比例以及部分氯代烃循环的方法控制产物中一氯代烃和多氯代烃的含量。取代氯化的典型例子是甲烷与氯的逐级取代氯化制取一氯甲烷、二氯甲烷、三氯甲烷和四 氯化碳的反应。
2 加成氯化
含有不饱和键的烃与氯进行加成氯化生成二氯化物,这类反应也是工业上制取氯代烃的重要方法之一。加成氯化也是放热反应,反应可在有催化剂或无催化剂条件下进行,FeCl
3、ZnCl
2、PCl
3等常用作催化剂。有催化剂存在下烯烃的加成氯化可在气相或液相中进行。
气相反应时,取代氯化和加成氯化同时发生,二者比例取决于操作条件,高温有利于取代氯化;增加原料中氯/烯烃的比例有利于加成氯化的进行。典型的工业过程是乙烯与氯加成生成1,2-二氯乙烷、乙炔与氯加成生成1,2-二氯乙烯的反应。
3 氢氯化反应
氢氯化是氯化氢与不饱和键发生的加成反应。这类反应按离子反应历程进行,反应一般分为两步,第一步首先形成中间产物碳阳离子及氯离子,然后氯离子再加到氢原子最少的碳阳离子上(马尔可夫尼可夫规则),生成氯代烃。
重金属氯化物可作为氢氯化反应的催化剂,如HgCl
2等。反应的选择性好,副产物少。烯烃的氢氯化反应是弱放热反应。炔烃的氢氯化反应是较强的放热反应,乙炔和氯化氢反应生成氯乙烯的反应热约为101 kJ/mol。典型的工业过程是乙烯与氯化氢加成生成氯乙烷和乙炔与氯化氢加成生成氯乙烯的反应。通常以FeCl
3、ZnCl
2、CuCl
2等金属氯化物为催化剂,该反应亦有良好的选择性。
4 脱氯化氢反应
从饱和氯代烃中除去氯化氢是生产氯代烯烃的一种方法。典型的工业过程是从二氯乙烷生产氯乙烯和从四氯乙烷生产三氯乙烯。 脱氯化氢反应是吸热反应,热力学计算表明温度在250℃以上对反应有利。加热、金属氯化物和无机碱等能促进反应;氯和氧对反应有促进作用;烯烃和醇则抑制 反应。
5 氧氯化反应
以氯化氢为氯化剂,在氧存在下进行的氯化反应,称为氧氯化反应,工业上首先应用于苯酚的生产。由于氯化过程中生成大量氯化氢副产物,价格比氯低的多,其利用对氯代烃生产的经济性有显著的影响,这促进了氧氯化工艺的开发和应用。
烃的氧氯化反应有加成氧氯化和取代氧氯化两种类型,烯烃的氧氯化为加成氧氯化,除苯氧氯化制氯苯的反应外,甲烷、乙烷等烷烃的氧氯化都为取代氧氯化。烷烃的取代氧氯化比烯烃的加成氧氯化困难,发展较迟。
典型的工业过程是乙烯氧氯化制二氯乙烷,后者大量用于氯乙烯生产。其它的氧氯化工艺还有丙烯氧氯化制1,2-二氯丙烷、甲烷氧氯化生产甲烷氯化物、丙烷氧氯化等。
6 氯解反应
即全氯化过程。以烃或氯代烃为原料,在高温(600~900℃)非催化及氯过量的条件下碳-碳键断裂得到链较短的全氯代烃,该反应主要用于四氯化碳和四氯乙烯的生产。
上述6种制备氯代烃的反应中,氧氯化反应最为重要,本章将作重点讨论。
9.3 氯乙烯 9.3.1氯乙烯的性质和用途
常温常压下氯乙烯(vinyl chloride,CH
2=CHCl)是无色气体,具有微甜气味,微溶于水,溶于烃类、醇、醚、氯化溶剂和丙酮等有机溶剂中。
氯乙烯是易燃易爆物质,与空气混合能形成爆炸性混合物,高温或遇明火能引起燃烧爆炸。由于光和热可引发氯乙烯单体聚合,故储存时应避免日晒,常温下长时间储存应加入阻聚剂(如对苯二酚)防止其自聚,一般以液体状态储存和运输。
氯乙烯在工业上的主要应用是生产聚氯乙烯树脂,故常称其为氯乙烯单体(vinyl chloride monomer,VCM)。目前用于制造聚氯乙烯树脂的氯乙烯约占其产量的96%,少量氯乙烯用于制备氯化溶剂,主要是1,1,1-三氯乙烷和1,1,2 -三氯乙烷。
9.3.2 氯乙烯的生产方法

2 联合法和烯炔法

3 平衡氧氯化法
9.4 平衡氧氯化生产氯乙烯 
因此,除目的产物EDC外,产物中一般都含有氯乙烷、三氯乙烷、氯乙烯、四氯乙烯、四氯乙烷等等,只是随反应条件不同这些副产物的含量多少不同而已。副产物不但使EDC的收率降低,还会影响氯乙烯的质量和氯乙烯的聚合过程。因此,应促进加成反应,抑制取代反应。
一般认为乙烯和Cl
2的加成机理是亲电加成。在极性溶剂或催化剂等作用下氯分子发生极化或解离成氯正负离子,氯正离子首先与乙烯分子中的键结合,经过活化络合物再和氯负离子结合成二氯乙烷。以FeCl
3催化剂为例,亲电加成反应过程如下:

对于乙烯,取代反应的机理是游离基取代机理。氯分子在光、热或过氧化物的作用下首先解离为两个氯原子游离基,然后Cl从乙烯中置换出一个氢游离基H?,后者再和Cl
2作用又生成Cl,形成链锁反应。和乙烯类似,VC、EDC等分子中的H也可以被Cl取代,形成前述各种产物。可见,Cl是产生多氯化副产物的根源。因此,凡能阻止Cl的产生,利于形成Cl+的各种因素一般都能减少副产物。
9.4.1.2 直接氯化反应的影响因素
1 溶剂
因为在液相条件下Cl+易生成,所以在减少多氯化物方面,液相反应比气相反应有利。而且,乙烯氯化反应是强放热反应,液相反应有利散热优于气相反应。在极性溶剂中,氯分子易发生极化,因此应选择极性溶剂,一般以产物EDC本身作溶剂。
因为1,2-二氯乙烷介电常数较大(10.65),可使氯原子间作用力减弱,利于氯分子离解,促进亲电加成反应。而且,1,2-二氯乙烷具有极性,对中间活性络合物的溶剂化作用强,对加成反应也有利。
2 温度
不论在气相还是在液相,温度越高,越有利于取代反应,多氯化物越多。这是因为温度越高,越有利于Cl?生成,同时使EDC和乙烯的取代反应活性趋同。对乙烯而言,反应温度低于250
0C,主要进行加成反应;反应温度为250-350
0C,取代反应剧烈;反应温度高于400
0C,主要发生取代反应。
3 催化剂
根据前面的分析,在液相条件下,为了加强加成反应的优势,一方面应抑制氯自由基的形成,另一方面可以使用能使氯分子解离为氯正离子的催化剂,常见的有 Al、Fe、P、Sb、S的氯化物和I2等。而非催化气相反应一般以自由基Cl?加成反应机理进行,Cl?的产生靠热能,需较高温度,因而使反应产物复杂 化。
因此,虽然直接氯化反应可在无催化剂条件下进行,但为了促进加成反应,抑制多氯化物,采用催化剂为好,目前工业上均采用FeCl
3催化剂。
由于二氯乙烷的作用,反应过程中氯化铁在溶剂中形成二聚体,该二聚体在铁的中心占有自由配位,使氯在催化剂上的吸附较困难,反应速率降低。添加NaCl助 催化剂能改善催化剂的性能。NaCl作用于二聚体,使其破裂后形成四氯化铁负离子配位体,增加主反应的反应速率,减少副反应的发生。
一般情况下,催化剂用量越多,反应速率和选择性越高。但催化剂在二氯乙烷中的溶解度有限,过多的催化剂会造成设备的堵塞。因此,保持合适的催化剂用量是必要的;同时要保证催化剂在溶剂中分布均匀。
4 原料配比
乙烯直接氯化反应是气液反应,反应物乙烯和氯气需由气相扩散进入二氯乙烷液相,然后在液相中进行反应。乙烯直接氯化是快速反应,因此反应速率和选择性取决 于乙烯和氯气的扩散溶解特性,液相中乙烯浓度大于氯气的浓度有利于提高反应的选择性。由于相同条件下,乙烯较氯气难溶于二氯乙烷,因此乙烯稍过量为好,有 助于减少多氯化物的生成,且过量乙烯较易处理。若Cl
2过量,取代反应几率增加,多氯化物增多。并且,Cl
2过量还会造成后续净化工序的设备腐蚀。一般为抑制取代反应,减少多氯化物,乙烯过量5~25%。
5 杂质
在高温氯化反应中氧气可能与乙烯中的氢原子反应生成水,而水与三氯化铁反应产生盐酸而使催化剂浓度发生变化,并对设备造成腐蚀;硫酸根和催化组分中的阳离 子反应,影响催化剂的用量和反应的选择性。因此,应严格控制原料气中氧气、水分和硫酸根的含量,要求氧气和水含量小于5×10
-5、硫酸根含量小于2×10
-6。

9.4.2 乙烯氧氯化反应
9.4.2.1 热力学分析
乙烯氧氯化体系中的主反应是生成1,2-二氯乙烷。除生成EDC的主反应外,还有许多可能的副反应。主反应如下:

主、副反应的平衡常数值都很大,在热力学上都是有利的,要使反应向生成1,2-二氯乙烷的方向进行,必须使主反应在动力学上占绝对优势,关键在于使用合适的催化剂和控制合适的反应条件。
9.4.2.2 反应机理和动力学
目前对乙烯氧氯化的反应机理主要有两种不同看法。一种认为是氧化-还原机理,另一种认为是环氧乙烷机理。
1 氧化-还原机理
该机理的反应过程包括下列三步反应。
第一步 吸附的乙烯与催化剂氯化铜作用生成1,2-二氯乙烷,氯化铜被还原为氯化亚铜:

第二步 氯化亚铜被氧气氧化成二价铜,并形成含有氧化铜的络合物:

第三步 氧化铜的络合物与氯化氢作用,生成氯化铜和水:

提出这一机理的主要依据是:
(a) 乙烯单独通过氯化铜催化剂时有EDC生成,同时氯化铜被还原为氯化亚铜;
(b) 将空气或氧气通过被还原的氯化亚铜时,氯化亚铜可全部转变为氯化铜;
(c) 乙烯的浓度对氧氯化反应速率的影响最大。
2 环氧乙烷机理
该机理认为乙烯的氧氯化反应经过中间物环氧乙烷,包括以下三个步骤。
第一步,反应物的吸附
乙烯在催化剂活性位s1上吸附:

氧气在催化剂活性位 上解离吸附:

氯化氢在催化剂活性位s2上吸附:

第二步,表面化学反应
吸附的乙烯和吸附的氧反应生成吸附的环氧乙烷中间物:

吸附的环氧乙烷中间物和吸附的氯化氢反应生成吸附的产物:

第三步,产物的脱附


其中控制步骤是吸附态乙烯和吸附态氧间的化学反应,即通常所说的表面反应控制。提出此机理的主要依据是氧氯化反应速率随乙烯和氧的分压增大而增大,与氯化氢的分压无关。
对乙烯氧氯化反应的动力学国内外研究很多,但所得到的动力学方程的形式各不相同,原因是动力学方程与催化剂的制备方法、催化剂中活性组分的含量、反应条件等多个因素有关。一般动力学方程的共同规律是,乙烯氧氯化反应速率随乙烯浓度增加而增加,与氯化氢的浓度无关。
9.4.2.3 催化剂
常用的氧氯化催化剂是金属氯化物,其中氯化铜活性最高,选择性最好。工业上普遍采用的载体是?-Al2O3,因为用 它作载体的CuCl2型催化剂比用SiO2、硅藻土等载体时活性温度降低,而且对于流化床反应器,Al2O3载体的流化性能好,耐磨性好,可减少催化剂粉 化流失。
根据氯化铜催化剂的组成,乙烯氧氯化催化剂分为以下三种类型。
1 单组分催化剂
这种催化剂也称为单铜催化剂,其活性 组分为氯化铜,载体为?-Al2O3,其活性与氯化铜的含量有直接关系。活性组分铜含量增加,催化剂的活性明显提高,但副产物CO2的收率也缓慢增加,表 明催化剂的选择性逐渐降低。在铜含量为5-6%(wt)时,氯化氢的转化率接近100%,催化剂的活性达到最高值。继续增加铜含量,催化剂的活性维持恒 定。因此工业用CuCl2/?-Al2O3的铜含量控制在5%左右。
CuCl2/?-Al2O3催化剂的缺点是,在反应条件下活性组分氯化铜易升华流失导致催化剂活性下降。反应温度愈高,氯化铜的升华愈快,催化剂活性下降愈迅速。
2 双组分催化剂
为 了改善单组分催化剂的热稳定性和使用寿命,在CuCl2/?-Al2O3基础催化剂上添加第二组分。常用的为碱金属或碱土金属氧化物,主要是氯化钾。对添 加氯化钾的催化剂,在铜含量相同的条件下,达到最高活性的温度随催化剂中钾含量增加而提高。添加少量KCl,既能维持CuCl2/?-Al2O3原有的低 温高活性特点,又能抑制CO2的生成。增加氯化钾用量,对选择性没有影响,但使催化剂活性迅速下降。氯化钾的作用至今尚未完全清楚。
3 多组分催化剂
为 进一步改进催化剂性能,特别是在较低操作温度下具有高活性的催化剂,近年来乙烯氧氯化催化剂向多组分方向发展。较有希望的是在CuCl2/?-Al2O3 催化剂基础上,同时添加碱金属氯化物和稀土金属氯化物。这种催化剂具有较高的活性和较好的热稳定性,反应温度一般在260?C左右。在此温度下,氯化铜很 少挥发,没有腐蚀性,且反应选择性良好。
9.4.2.4 反应条件的确定
1 温度和压力
温度对乙烯氧氯化反应的选择性有很大影响。反应温度过高,选择性下降,产物中一氧化碳和二氧化碳含量升高。同时副产物三氯乙烷也会增高。
过 高的温度对催化剂也有不良影响,这是因为活性组分氯化铜的升华损失随温度升高而加剧,从而导致催化剂寿命缩短。乙烯氧氯化反应是强放热反应。从生产安全角 度考虑,必须对反应过程的温度进行严格控制。综合分析结果,反应温度控制得低一些为好。最适宜的操作温度范围与使用的催化剂有关。当使用高活性的氯化铜催 化剂时,最适宜的温度范围是220-230?C左右。
随着压力增加,反应选择性下降。因此,操作压力不宜过高,通常在1MPa以下,流化床反应器压力宜低,固定床反应器压力可稍高。
2 原料配比
从 氧氯化的动力学可知,提高原料气中氧,特别是乙烯的分压对反应有利。乙烯和氧过量除可增大主反应速率外,还有一个重要的目的,就是尽可能使氯化氢完全转 化,因为氧氯化反应伴有水生成,若氯化氢转化不完全,大量未反应的氯化氢和水结合生成盐酸,造成设备腐蚀,如果乙烯过量,可使氯化氢接近完全转化。另外, 如果氯化氢过量,则过量的氯化氢将吸附在催化剂的表面上,使催化剂颗粒膨胀。对于流化床反应器的操作,催化剂颗粒膨胀使床层迅速升高,甚至产生节涌等不正 常现象。
氧氯化的副反应主要是燃烧反应和深度氯化反应。对于深度氯化反应,乙烯过量是有利的,可抑制多氯化物的生成。但对于燃烧反应,在氯化氢高 转化率区,随氯化氢浓度增大而减弱,随乙烯和氧的浓度增大而加剧,因此乙烯不可过量太多,否则将加剧燃烧反应,使尾气中碳氧化物含量增多。同理,氧气稍有 过量对反应有利,过多也加剧燃烧反应。因此工业操作采用乙烯稍过量,氧气过量大约50%,氯化氢则为限制组分。按照化学计量式C2H4?HCl?O2= 1?2?0.5,典型工业操作的原料配比则为C2H4?HCl?O2=1.05?2?0.75。
3 原料的纯度
原料乙烯的纯度对氧氯化反应影响很小,因此氧氯化反应可用浓度较低的乙烯,例如使用含70%乙烯和30%惰性组分的原料,其中惰性组分可以是饱和烃也可以是氮气。氮气、烷烃等惰性气体对氧氯化反应无影响,还能带走反应热,使反应系统的温度较易控制。
但原料乙烯中的不饱和烃,如乙炔、丙烯和丁烯等的含量必须严格控制,这些烃类的存在不仅会使氧氯化反应产物二氯乙烷的纯度降低,而且会对二氯乙烷的裂解过 程产生不利影响。原料氯化氢的纯度也很重要,当采用二氯乙烷裂解产生的氯化氢时,其中很可能含有乙炔,必须将其除掉。通常是采用加氢精制,使乙炔含量控制 在2?10-4以下。
4 空速
空速对乙烯氧氯化反应转化率有强烈影响。要使氯化氢接近完全转化,必须有较长的接触时间,但接触时间过长, 氯化氢转化率反而下降。此现象很可能是由于接触时间过长而发生了连串副反应,产物二氯乙烷裂解为氯乙烯和氯化氢。所以,乙烯氧氯化反应有一个适宜的空速, 此适宜的空速取决于所采用的催化剂。活性低的催化剂,适宜空速较低,活性好的催化剂,适宜空速较高。一般范围为250-350 h-1。
9.4.3二氯乙烷热裂解反应
9.4.3.1 反应原理
化合物的热裂解反应活性与键能大小有关,一般键能相差愈大,裂解反应选择性 愈好。二氯乙烷分子中三种键的键能大小顺序是:C-H﹥C-C﹥C-Cl,受热后C-Cl最易断裂,C-H键最难断裂。但是三种键的键能和热裂解活化能相 差并不大,在C-Cl发生断裂的同时,C-C键也会发生某种程度的断裂,随之发生各种副反应。除断链反应外,还有异构化、芳构化、聚合、完全分解等反应。 因此裂解过程十分复杂,既包括一次反应也包括二次反应,EDC裂解的主要反应如下。

上述8个反应中生成氯乙烯、苯、氯丁二烯和氯甲烷的反应在热力学上有利,其中苯是由二次反应生成的,第一步氯乙烯断链脱氯化氢生成乙炔,第二步乙炔芳构化生成苯,第一步反应在热力学上不利,但是一旦生成乙炔则很容易生成苯。其余反应的 >0,热力学不利。
一般认为主反应按游离基链式机理进行,第一步为游离基产生反应,是整个反应的控制步骤,第二、三步为链传递反应,第四步反应为游离基中止反应。
无催化剂存在时,热裂解反应约于400?C开始,500?C变得显著。工业上反应一般在500-600?C进行。
温 度对热裂解的选择性有很大影响,温度升高,裂解反应选择性下降。为了降低裂解温度,提高裂解选择性,可进行催化裂解。一般,催化裂解可比非催化裂解降低反 应温度50-100?C。Cr、Fe、Zn、Ag、Cu、Cd、、Ba、Sr等的氯化物,活性炭、分子筛和SiO2等均有催化活性。
采用光催化或加入少量引发剂也可加快裂解速度,降低反应温度,减轻析碳结焦,CCl4、Cl2、O2、CCl3COOH等具有引发作用。
9.4.3.3 反应条件的确定
1 温度
二氯乙烷裂解生成氯乙烯和氯化氢是可逆吸热反应,提高反应 温度对裂解反应的热力学和动力学都有利。对于二氯乙烷裂解反应,当温度低于450?C时,反应的转化率很低;当温度升高至500?C时,转化率明显提高, 温度在500-550?C范围内,温度每升高10?C反应转化率可增加3-5%。但温度过高,二氯乙烷深度裂解、产物氯乙烯分解和聚合副反应也加速。当温 度超过600?C时,副反应速率大于主反应速率。因此确定反应温度要综合考虑二氯乙烷转化率和氯乙烯收率两个因素,通常选在500-550?C范围内。
2 压力
二 氯乙烷裂解是体积增加的可逆反应,从热力学角度考虑提高压力对反应不利。但从动力学角度考虑,增加压力可提高反应速率和设备的生产能力。并且压力提高可使 气体密度增加,有利于抑制二氯乙烷分解析碳反应;改善气体的导热性能,这些均有利于提高产物氯乙烯的收率。同时,增加压力有利于产物氯乙烯和副产氯化氢的 冷凝回收,因此实际生产中都是采用加压操作。目前生产中有低压法(?0.6 MPa)、中压法(?1.0 MPa)和高压法(?1.5 MPa)三种工艺。
3 原料纯度
原料二氯乙烷含有杂质对裂解反应有不利的影响,其中最有害的杂质是抑制剂,可减慢裂解反应速度和促进结 焦。危害最大的抑制剂是1,2-二氯丙烷,其含量为0.1-0.2%时即可使二氯乙烷转化率下降4?10%,原因是二氯丙烷分解生成的氯丙烯具有更强的抑 制作用。因此要求原料中二氯丙烷的含量小于0.3%。此外,三氯甲烷、四氯化碳等多氯代烃对二氯乙烷裂解反应也有抑制作用。铁离子也会加速二氯乙烷深度裂 解副反应,故要求铁离子含量不超过10-4。为了减少物料对反应炉管的腐蚀,要求水分含量低于5?10-6。因此,工业生产中对EDC纯度要求很高,一般 为99%以上。
4空速
物料在反应器内的停留时间愈长,二氯乙烷的转化率愈高。但是,停留时间过长会使结焦积碳副反应迅速增加,导致氯乙烯的产量下降。
9.5 乙烯氧氯化生产氯乙烯工艺 平衡氧氯化法生产氯乙烯工艺主要包括直接氯化单元,氧氯化单元,二氯乙烷净化单元,二氯乙烷裂解单元和氯乙烯精制五个单元。其中,二氯乙烷精制和氯乙烯精 制单元各大公司的技术基本相同,直接氯化和氧氯化两个单元各公司采用的技术则不尽相同。在直接氯化单元主要有低温氯化工艺和高温氯化工艺;在氧氯化单元有 固定床工艺和流化床工艺,根据所采用的原料气是空气或氧气,又分为空气法和氧气法。二氯乙烷裂解单元区别不大,主要有气相进料和液相进料之别。乙烯平衡氧 氯化法制氯乙烯的工艺流程示意图见图9-4。

9.5.1 直接氯化单元
乙烯直接氯化大多采用三氯化铁催化剂,在液相、常压下进行。为使进入反应器的氯气完全转化,控制乙烯加料量较理论量过剩3-5%。该单元包括乙烯直接氯化 反应、EDC酸洗和碱洗。酸洗的目的是除去氯化反应产物中的氯化铁,以防止碱洗时形成氢氧化铁,在EDC精制时堵塞轻组分和重组分塔的塔釜。碱洗主要是处 理游离氯、氯化氢和三氯乙醛,防止下游设备的腐蚀,以及三氯乙醛和EDC在轻组分塔中形成共沸物。
直接氯化反应在气液塔式反应器中进行。反应器为内衬瓷砖的钢制设备,反应器中央安装套筒内件,套筒内填装铁环填料。反应器外安装两台外循环冷却器,将反应 热及时移出反应区。原料乙烯、氯气与循环的二氯乙烷经混合喷嘴混合后从氯化反应器底部通入,补充三氯化铁催化剂用二氯乙烷溶解后送入反应器,反应器中催化 剂的浓度要求控制在2x10
-4左右。随着反应的进行,产物二氯乙烷不断地从反应器的支管流出经过滤器过滤后进入粗二氯乙烷洗涤分 层器。反应产物在两级串联的洗涤分层器内经酸洗和碱洗,除去其中少量的三氯化铁催化剂和氯化氢等,得到的粗二氯乙烷送入储罐准备去精馏。洗涤废水经回收二 氯乙烷后送废水处理工序,从反应器处来的惰性气体经冷凝回收二氯乙烷后送入废气处理工序。
根据产物的出料方式,直接氯化分为低温氯化、中温氯化和高温氯化技术。低温氯化是在EDC沸点(83.5
0C)以下进行反应,粗EDC产品液相采出,中温氯化是在EDC沸点以上进行反应,反应温度通常为90-100
0C,生成的EDC以气相出料,经冷凝器冷凝后大部分回流移去反应热。高温氯化也是在EDC沸点以上进行反应,反应温度为120
0C左右,压力为0.2-0.3 MPa。由于反应是在液相沸腾条件下进行,未转化的原料乙烯和氯气会被生成的二氯乙烷蒸气带走而使产物收率下降。为了解决这个问题,高温氯化采用带分离器的环流反应器。
9.5.2 乙烯氧氯化制二氯乙烷
根据氧氯化采用的氧化剂是空气还是纯氧,分为空气法和氧气法。
来自二氯乙烷裂解的氯化氢气体经加氢反应器加氢除掉炔烃后与乙烯混合进入氧氯化反应器,空气从反应器底部进入,在分布器上与乙烯、氯化氢混合后进入反应器,通过调节高压蒸汽罐的压力控制反应温度。自反应器顶部出来的反应混合气中含有二氯乙烷、水、CO、CO
2和 其它少量的氯代烃类,以及未转化的乙烯、氧、氯化氢及惰性气体。未反应的混合气体和产物经骤冷塔,用水逆流喷淋以吸收其中的氯化氢,同时洗去混合物中尚余 存的少量的催化剂颗粒。此时,产物二氯乙烷和其它氯的衍生物仍然存在气相中。骤冷塔顶引出的混合气经热交换器,其中冷凝成液态的二氯乙烷经碱洗水洗后进二 氯乙烷储罐,未凝气体进吸收塔,以煤油吸收其中尚存的二氯乙烷,尾气排出系统,吸收剂解吸后回收利用。骤冷塔塔底排出的水,其中含有盐酸及少量二氯乙烷, 经碱液中和后送入汽提塔,以水蒸气汽提,回收其中的二氯乙烷,冷凝后送入分层器。
在氧氯化技术发展过程中,固定床和流化床反应器是并存的。 固定床反应器的优点是转化率高,但传热较差,易产生局部温度过高而使反应的选择性下降,并使催化剂活性下降较快,寿命缩短。流化床反应器由于床内固体颗粒 粒度较小,又是分散在气流中,气固相间的接触面积大,使传热传质优良,床层内温度分布均匀,因此具有不产生热点、控温容易的优点。缺点是催化剂的磨损较 大,物料返混严重。在氧氯化技术开始发展时,转化率仅达70-80%。随着催化剂的改进和流化床技术的进步,其转化率已达到或超过固定床水平,氯化氢和乙 烯转化率分别可达99%,成为氧氯化反应器的发展方向。
9.5.3 二氯乙烷净化
作为生产氯乙烯的中间体,对二氯乙烷的质量要求是 无水、无铁。由乙烯直接氯化及氧氯化过程所得到的产物二氯乙烷中含一定数量的杂质,裂解前需除去。二氯乙烷精制流程有3塔、4塔和5塔3种方案。其中4塔 流程是最常规的流程,由脱水塔、低沸塔、高沸塔和回收塔组成。脱水塔是利用少量EDC和水形成共沸物的原理将水从液体中脱除。低沸塔和高沸塔分别将EDC 中的轻、重组分分离,回收塔是进一步将高沸物中的EDC回收。
9.5.4 二氯乙烷裂解
裂解是将EDC转化为VCM和氯化氢的过 程,有气相法和液相法两种,工业上采用气相法。由于热裂解的反应器结构简单,又不需要催化剂,且EDC转化率和氯乙烯收率与催化裂解法基本相同,因此受到 普遍欢迎。二氯乙烷热裂解在管式炉内进行,炉型构造与烃类热裂解所用管式炉构造相似。炉体由对流段和辐射段组成,在对流段设置原料预热管,反应管设置在辐 射段。二氯乙烷裂解反应是强吸热反应,靠管外燃料燃烧加热提供反应所需要的热量。
用定量泵将精二氯乙烷送入裂解炉的预热段,借助裂解炉烟气加热到220
0C左右,部分二氯乙烷气化。将所形成的气液混合物送入分离器,自分离器底部引出未气化的二氯乙烷,经过滤器进蒸发炉进行气化,气化后的二氯乙烷再经过分离器分出其中所夹带的液滴。分离器顶部引出的气相二氯乙烷进入裂解炉的辐射段,于500-550
0C进行裂解反应生成氯乙烯和氯化氢。为了减少裂解过程的副反应,一般控制裂解转化率为50-55%,最高可达60%。
9.5.5 氯乙烯精制
来自二氯乙烷裂解单元的氯乙烯中含有少量未转化的二氯乙烷和产物氯化氢,氯乙烯精制的目的是除掉这些杂质,得到聚合级的氯乙烯单体。氯乙烯精馏工艺有5种,最常用的是两塔流程和3塔流程。
3塔流程中包括氯乙烯精馏塔、气提塔和氯化氢塔。氯乙烯精馏塔的塔顶压力为0.5MPa,塔顶温度为40
0C,塔顶采出为氯乙烯,其中含少量氯化氢,经冷凝后进汽提塔。精馏塔塔釜液组成主要为二氯乙烷,送二氯乙烷净化单元作为高沸塔进料,进一步回收二氯乙烷。
汽提塔的作用是将产品氯乙烯中所含的少量氯化氢汽提出来。该塔塔釜出料为氯乙烯,其中仅含微量氯化氢,进中和塔中和后氯化氢含量降至10
-6以下,作为生产聚氯乙烯的原料。汽提塔的塔顶采出为含氯化氢的氯乙烯,进氯化氢塔回收其中的氯化氢。
9.6 平衡氧氯化法技术进展 9.6.1 新反应路线
1乙烷直接氧氯化工艺
乙烷氧氯化制VCM工艺将乙烷直接转化为氯乙烯,乙烷的价格比乙烯便宜,乙烷直接转化为氯乙烯具有强大的生命力和工业化价值。乙烷直接转化制氯乙烯的3种基本反应为:

第二个反应即乙烷的氧氯化反应,不产生难以利用的氯化氢,是最具吸引力的替代方法。乙烷氧氯化制氯乙烯的技术关键是开发高活性和高选择性的催化剂。
2 乙烯直接氯化/氯化氢氧化
除联合法和平衡氧氯化法外,在氯乙烯生产中平衡利用氯化氢的第三种方法是将氯化氢催化氧化转化为氯气,再将产生的氯气返回到直接氯化单元用于乙烯的氯化,整个工艺中无乙烯氧氯化单元。
新工艺中,乙烯直接氯化生成EDC;EDC热裂解生成氯乙烯和氯化氢;氯化氢经空气或氧气氧化为氯气,氯气用于乙烯的直接氯化,整个工艺不副产氯化氢。由 于EDC都是在直接氯化反应段生成,氯乙烯总收率高,产品纯度高,不需碱洗和精制就可进行热裂解,且反应过程不产生水,避免了设备的腐蚀问题。
近年来,氯化氢氧化法取得重大进展。南加利福尼亚大学在雷通公司(Raytheon Co.)的支持下合作开发了一种氯化氢两段催化氧化工艺,并建成了一套半工业化生成装置。该工艺在催化剂和反应器方面均有独到之处。在催化剂方面,以分子 筛为载体、氯化铜和氧化铜为活性组分,提高了催化剂的活性和寿命;在反应器方面,采用两段沸腾床反应器。
清华大学反应工程实验室开发了氯化氢两段催化氧化的挡板流化床工艺。该工艺在流化床提升管中设置气固分布板形成两段流化床反应器,上段进行氯化反应,下段进行氧化反应。
3 乙烯直接取代氯化
乙烯也能够与氯气发生取代反应直接生成氯乙烯,分子轨道理论分析结果表明,乙烯C-H键的活化对乙烯的取代氯化反应非常重要,凡能活化乙烯C-H的物质均 对乙烯直接取代氯化反应有催化作用,溶剂对催化剂的活性也有很大影响。乙烯取代氯化合成氯乙烯的主催化剂为氯化钯,助催化剂为四氯苯醌,在100
0 C、2.0MPa、乙烯过量条件下,转化率可达80%,但选择性不高。该法的优点是反应步骤较加成氯化少,不需要二氯乙烷的裂解反应直接可得氯乙烯。但需提高转化率和选择性,才能具有工业利用价值。另外,该法也存在氯化氢的平衡利用问题。
4 其它方法
道化学公司研究以氯化氢代替氯气作氯源制氯乙烯:

研究工作所采用的催化剂为MOCl,其中M为Sc、Y或镧系金属,反应温度400-420
0C,VCM的选择性最高可达到77%。
日本学者曾提出,将放热的乙烯加成氯化反应和吸热的二氯乙烷裂解反应合并在一个反应器中进行,即氯化裂解反应,从而缩短工艺流程,合理利用反应热。但氯化裂解反应需在410-480
0C下进行,高的反应温度使结焦等副反应增加,VCM收率下降。
9.6.2 平衡氧氯化法
1 乙烯氧氯化催化剂
乙烯氧氯化制二氯乙烷是平衡氧氯化法生产VCM的关键步骤,其核心是催化剂,因此,有关固定床和流化床氧氯化催化剂的研究从未间断。
Geon公司近年来对添加助催化剂的多组分乙烯氧氯化催化剂进行了大量研究,研制出含Cu、K、Mg的三组分和含Cu、K、Mg、Ce的四组分?-Al
2O
3负载催化剂。实验室流化床反应器评价表明,添加Mg和Ce的多组分催化剂,氯化氢转化率、 EDC选择性和热稳定性均高于通常的单组分和双组分催化剂。这种新型催化剂却可以在高乙烯转化率下同时获得高的氯化氢转化率和EDC选择性。
意大利Montecatini公司近年来在固定床乙烯氧氯化催化剂的研制有不少突破。其研制的中空圆柱状催化剂和三通道中空圆柱状催化剂均具有较好的反应性能。
欧洲乙烯公司开发了新型固定床氧氯化催化剂。新型催化剂由铜、碱金属、碱土金属、ⅢB族金属和镧系元素组成,采用特殊技术(浇铸)制成空心圆柱型。具有传热性能好、流动阻力低的特点。
德古赛(Degussa)公司开发了一种乙烯氧氯化制EDC的催化剂,该催化剂含有Cu
2+化合物、一种或多种碱金属化合物、原子序数为57-62的稀土金属氧化物和氧化锆四组分,载体为?-Al
2O
3,具有热稳定性好、低温活性高、选择性好和机械强度高的特点。
国内石油化工科学研究院、北京化工研究院、上海氯碱公司等多家单位也在研究乙烯氧氯化单铜和多组分催化剂,其中一些催化剂的性能与国外水平相近。
2 氧氯化反应器
国外采用固定床氧氯化工艺的有EVC公司、Dow公司和BASF公司等,目前固定床氧氯化体系正由三级串联向双级串联和单反应器型式发展。
一般,氧氯化反应的温度不得超过285
0C, 否则催化剂的活性和反应的选择性均下降,因此采用两级串联或单个固定床反应器的最大难点是如何控制反应器的热点温度。EVC公司采用新型催化剂填充方式、 在总物料配比相同的条件下调整每级反应器进料气中氧气浓度和加入惰性气体的方法,实现了两级固定床串联和单个固定床反应器氧氯化反应工艺。在两级串联工艺 中,每级反应器的催化剂分三段装填,三层催化剂的高度需严格控制,以保证每个反应器的热点温度均不超过允许值。
采用单个固定床进行氧氯化反应,除催化剂活性需沿物流方向合理分布外,还需调整原料配比,使乙烯相对于氯化氢大大过量,这样有利于移除反应热和提高反应选择性。过量的乙烯可循环利用或用于直接氯化反应。
3 直接氯化工艺和反应器
最近,伍德公司开发带循环回路的沸腾反应器技术用于乙烯直接氯化生产二氯乙烷,在新型反应器中,氯化反应主要发生在U型外循环回路的提升段。由于乙烯的溶 解特性对直接氯化反应有较大的影响,而现有工艺是先将氯气溶解在溶剂EDC中,然后与乙烯混合进行反应,这样容易造成局部氯过量,增加高氯副产物,对反应 选择性不利。该工艺的改进之一是将乙烯和氯气分别溶于EDC后在80-120
0C、 0.1-0.25 MPa、无机铁络合物催化剂作用下进行反应。另一个改进是增加了乙烯在提升段下部的循环回路,以提高EDC中乙烯的浓度。同时,将产品回收器中的EDC进 行二次冷却后溶解氯气,以增加其溶解度。新工艺的特点是,副产物少,EDC的纯度可达99.93%,不需精馏精制即可直接用作裂解原料。
4 EDC裂解工艺
Borsa等利用各种仪器分析手段研究了EDC裂解过程中焦体的生成机理,发现EDC裂解结焦是由于EDC气化过程中在气相主体中形成了高沸点的结焦前驱 体和焦油液滴,这些高沸点物质凝结并碰撞到炉管壁面造成结焦。同时,由于EDC的部分气化,使液相EDC中杂质浓度增加,也加速结焦。就是说,如果在 EDC裂解过程中不形成气相EDC,则可有效地减少结焦。伍德公司开发了一种新的EDC裂解工艺,与传统工艺不同的是,先将EDC加压到临界压力 (5.36 MPa),然后在临界压力下将EDC加热到临界温度(288
0C),这样在整个EDC预热过程中,始终未产生相变,且液相中溶解的杂质浓度没有变化,有效地避免了结焦的生成。
5 其它
在平衡氧氯化法中,直接氯化和氧氯化都是强放热反应,因此采用热耦合技术合理利用反应热是平衡氧氯化法的一个研究热点。低温氯化的优点是副反应少、EDC 纯度高,但反应热无法利用。为解决这一矛盾,伍德公司开发低温氯化利用反应热的技术。在该技术中,靠EDC的汽化移出反应热,汽相EDC压缩后用于轻组分 塔、重组分塔和真空塔再沸器的热源。
http://202.113.13.67/courses/chemtech/edutools.php?tid=342
https://blog.sciencenet.cn/blog-3913-13186.html
上一篇:
《工业催化原理》精品课程——厦门大学下一篇:
2007年化学学科重大进展、发现